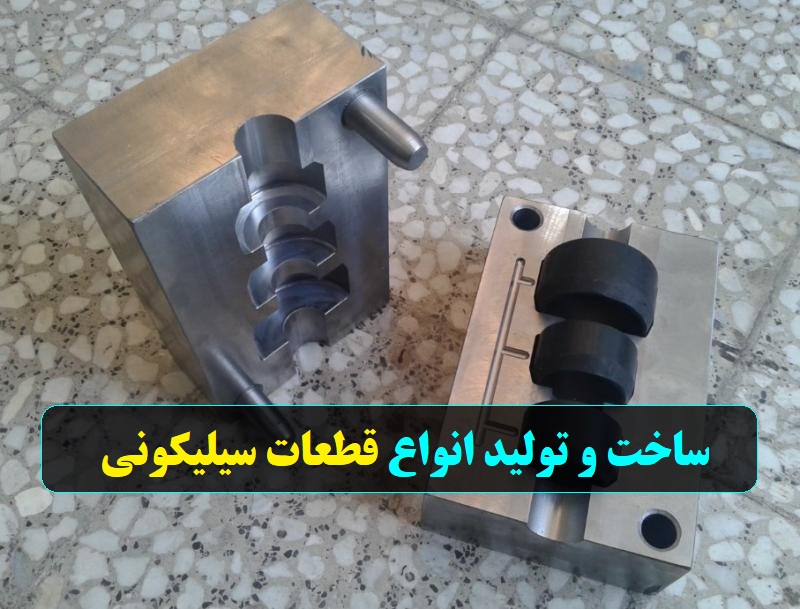
تولید کننده انواع قطعات لاستیکی و سیلیکونی : پیشگامان انعطاف و دوام | شرکت [پارس بسکت ] پیشرو در عرصه طراحی و تولید انواع قطعات لاستیکی و سیلیکونی با کیفیتی بی نظیر و برآورده سازی دقیق نیازهای صنایع گوناگون است. ما با تکیه بر دانش و تجربه متخصصان مجرب و بهره مندی از تکنولوژی های پیشرفته، طیف وسیعی از محصولات را مطابق با بالاترین استانداردهای بین المللی و نیازهای سفارشی مشتریان ارائه می دهیم.
با سلام به وبسایت رسمی شرکت پارس بسکت تولید کننده انواع قطعات صنعتی خوش آمدید. لطفا جهت ثبت سفارش یا آگاهی از قیمت محصولات خود کافیست راهنمای ارتباطی زیر را مطالعه فرماید با تشکر از همراهی شما.
ساعت تماس از 9 صبح تا 6 غروب
توجه در ساعات غیر کاری نیز sms ارسال کنید.
همچنین در صورت مشاهده هر گونه مشکل فنی در سایت و ارتباط با مدیران فروش پارس بسکت با مسئول فنی سایت تماس بگیرید.
برای ثبت سفارس بر روی دکمه واتساپ کلیک کنید.
پیشتازان نوآوری و کیفیت در دنیای پلیمرها
✔ طیف گسترده ای از محصولات: واشر، اورینگ، گسکت، دیافراگم، ضربه گیر، کوپلینگ، تسمه نقاله، قطعات صنعتی و بهداشتی و … تنها بخشی از محصولات متنوع ما هستند.
✔ انعطاف پذیری در تولید: قابلیت تولید قطعات با اشکال ساده و پیچیده، ابعاد و ضخامت های مختلف و با متریال متنوع لاستیکی و سیلیکونی
✔ کیفیت و دوام بی همتا: استفاده از مواد اولیه مرغوب و رعایت دقیق فرآیندهای تولید، عمر طولانی و عملکرد بهینه قطعات را تضمین می کند.
✔ کنترل کیفی دقیق: آزمایشات و بازرسی های مستمر در تمامی مراحل تولید، اطمینان از انطباق کامل محصولات با استانداردهای کیفی را به اثبات می رساند.
✔ مشاوره تخصصی: کارشناسان ما با اشراف کامل بر خواص مکانیکی و شیمیایی انواع لاستیک و سیلیکون، مشاوره دقیق و انتخاب مواد متناسب با هر کاربرد را در اختیار شما قرار می دهند.
✔ سرعت و دقت در تحویل: ما متعهد به رعایت دقیق زمانبندی های تحویل و ارسال محصولات با بسته بندی ایمن و مطمئن هستیم.
کاربرد محصولات ما در صنایع مختلف:
- صنایع خودروسازی: قطعات موتور، درب ها و پنجره ها، سیستم های تعلیق
- صنایع نفت و گاز: تجهیزات حفاری، قطعات آب بندی، واشرهای مقاوم به فشار و دما
- صنایع پزشکی و دارویی: قطعات سیلیکونی برای تجهیزات و ابزارهای پزشکی
- صنایع غذایی و آشامیدنی: واشرها و درزگیرهای بهداشتی، لوله های انتقال مواد
- صنایع ساختمان و عمران: عایق های رطوبتی، درزگیرهای درب و پنجره، قطعات ارتعاش گیر
- دیگر صنایع: لوازم خانگی، صنایع برق و الکترونیک، صنایع نظامی و هوافضا
برتری انتخاب یک تامین کننده معتبر قطعات لاستیکی و سیلیکونی
انتخاب یک تامین کننده معتبر و باتجربه در این حوزه نه تنها بر کیفیت و عملکرد قطعات مورد استفاده، بلکه بر بهینه سازی هزینه ها و پیشبرد روان پروژه های شما تاثیر بسزایی دارد.
ما در [ شرکت پارس بسکت] با درک این اهمیت، همواره بر ارائه خدماتی فراتر از تامین قطعات تمرکز داریم. مشاوره تخصصی، انتخاب مواد و طراحی دقیق، کنترل کیفی سختگیرانه و پشتیبانی فنی مستمر، تنها بخشی از تعهدات ما در قبال مشتریان ارزشمندمان است با [پارس بسکت ]، کیفیت، انعطاف و دوام را به پروژه های خود هدیه دهید.
منتظر تماس شما برای همکاری های موفق و سازنده هستیم.
ساخت انواع قطعات سیلیکونی
ساخت انواع قطعات سیلیکونی : سیلیکون، مادهای پلیمری با خواص منحصر به فرد، انقلابی در تولید قطعات با انعطافپذیری و مقاومت بالا ایجاد کرده است. طیف گستردهای از صنایع، از پزشکی و خودروسازی گرفته تا لوازم خانگی و هوافضا، از مزایای قطعات سیلیکونی بهره میبرند. در این مقاله، به بررسی فرآیند ساخت انواع قطعات سیلیکونی، ویژگیهای مهم آنها و کاربردهای متنوع آنها در صنایع مختلف میپردازیم.
روشهای ساخت قطعات سیلیکونی:
دو روش اصلی برای ساخت قطعات سیلیکونی وجود دارد:
قالبگیری فشاری: در این روش، سیلیکون مایع تحت فشار به داخل قالبهای بسته تزریق میشود. پس از سفت شدن سیلیکون، قالب باز شده و قطعه نهایی خارج میشود. این روش برای تولید قطعات با تعداد بالا و پیچیدگی کم مناسب است.
قالبگیری تزریقی: در این روش، سیلیکون مایع با حرارت ذوب شده و سپس با فشار زیاد به داخل قالبهای داغ تزریق میشود. پس از سرد شدن، قطعه نهایی از قالب خارج میشود. این روش برای تولید قطعات با دقت ابعادی بالا و اشکال پیچیده مناسب است.
علاوه بر این دو روش، روشهای دیگری مانند ریختهگری، اکستروژن و چاپ سهبعدی نیز برای ساخت قطعات سیلیکونی استفاده میشوند. انتخاب روش مناسب، به شکل، اندازه، خواص مورد نیاز و تعداد قطعات مورد نظر بستگی دارد.
ویژگیهای مهم قطعات سیلیکونی:
- انعطافپذیری بالا: یکی از بارزترین ویژگیهای قطعات سیلیکونی، انعطافپذیری آنهاست. این ویژگی باعث میشود این قطعات در برابر ارتعاشات و ضربه مقاوم باشند و به راحتی با سطوح مختلف سازگار شوند.
- مقاومت در برابر دماهای بالا و پایین: قطعات سیلیکونی خواص خود را در طیف گستردهای از دماها، از دمای انجماد آب تا دمای بالای ۲۰۰ درجه سانتیگراد، حفظ میکنند. این ویژگی آنها را برای استفاده در تجهیزات پزشکی، لوازم خانگی و صنایع خودروسازی مناسب میسازد.
- عایق الکتریکی: سیلیکون، عایق الکتریکی خوبی است و به همین دلیل در ساخت قطعات الکتریکی و الکترونیکی مانند واشرها، درزگیرها و عایق سیمها مورد استفاده قرار میگیرد.
- مقاومت در برابر مواد شیمیایی: قطعات سیلیکونی در برابر بسیاری از مواد شیمیایی مانند روغنها، حلالها و اسیدها مقاوم هستند. این ویژگی آنها را برای استفاده در صنایع شیمیایی و غذایی مناسب میسازد.
- ایمنی زیستی: سیلیکون مادهای غیرسمی و غیرآلرژیزا است و به همین دلیل در ساخت تجهیزات پزشکی، ظروف نگهداری مواد غذایی و لوازم کودک مورد استفاده قرار میگیرد.
کاربردهای متنوع قطعات سیلیکونی:
همانطور که اشاره شد، قطعات سیلیکونی در صنایع مختلفی کاربرد دارند. در اینجا به چند نمونه از کاربردهای آنها اشاره میکنیم:
- صنایع پزشکی: لولههای تنفسی، پستانک، ایمپلنتهای پزشکی، واشرها و درزگیرهای تجهیزات پزشکی.
- صنایع خودروسازی: واشرها، درزگیرهای درب و پنجره، لولههای خنککننده، قطعات عایقبندی موتور.
- لوازم خانگی: واشرها و درزگیرهای اجاق گاز، ماشین لباسشویی و ظرفشویی، قطعات عایقبندی ظروف آشپزی.
- صنایع غذایی: واشرها و درزگیرهای ظروف نگهداری مواد غذایی، قطعات عایقبندی تجهیزات فرآوری مواد غذایی.
- صن صنایع الکتریکی و الکترونیکی: واشرها و درزگیرهای باتریها، عایق سیمها، قطعات عایقبندی تجهیزات الکترونیکی.
نتیجهگیری:
با توجه به انعطافپذیری بالا، مقاومت در برابر دما و مواد شیمیایی، عایق الکتریکی و ایمنی زیستی، قطعات سیلیکونی به انتخابی ایدهآل برای طیف گستردهای از صنایع تبدیل شدهاند. پیشرفتهای مستمر در فناوری تولید سیلیکون، نویدبخش توسعه مواد و قطعات جدید با خواص و کاربرد
با سلام به وبسایت رسمی شرکت پارس بسکت تولید کننده انواع قطعات صنعتی خوش آمدید. لطفا جهت ثبت سفارش یا آگاهی از قیمت محصولات خود کافیست راهنمای ارتباطی زیر را مطالعه فرماید با تشکر از همراهی شما.
ساعت تماس از 9 صبح تا 6 غروب
توجه در ساعات غیر کاری نیز sms ارسال کنید.
همچنین در صورت مشاهده هر گونه مشکل فنی در سایت و ارتباط با مدیران فروش پارس بسکت با مسئول فنی سایت تماس بگیرید.
برای ثبت سفارس بر روی دکمه واتساپ کلیک کنید.
تولید قطعات سیلیکون کارباید
سیلیکون کارباید، مادهای شگفتانگیز با ترکیب عناصر سیلیسیم و کربن، خواصی منحصربهفرد در برابر سایش، دما و فشارهای بالا ارائه میدهد. این ویژگیهای متمایز، سیلیکون کارباید را به گزینهای ایدهآل برای تولید قطعاتی بدل ساخته است که در شرایط سخت صنعتی، دوام و عملکردی بینظیر را به نمایش میگذارند.
اما خلق این قطعات شاهکار، فراتر از ترکیب سادهی دو عنصر نهفته است. سفری است از علم و فناوریهای پیشرفته تا هنر مهندسی دقیق، که در مسیر آن، خواص ذاتی ماده با تکنیکهای تولید هماهنگ شده و محصولی نهایی با کیفیتی کمنظیر متولد میشود.
سفری در ژرفای فرآیند تولید
روشهای متعددی برای تولید قطعات سیلیکون کارباید وجود دارد که هر یک، مزایا و معایب خاص خود را داراست. مهمترین این روشها عبارتند از:
- پرسکرد گرم و فشرده (HP):: در این روش، پودر سیلیکون کارباید با افزودنیهای مناسب در قالبهای مخصوص پرس شده و تحت حرارت بالا قرار میگیرد تا به تراکم و استحکام مطلوب برسد. این روش برای تولید قطعات ساده با اشکال اولیه مناسب است.
- پرس ایزواستاتیک گرم (HIP): روشی پیشرفتهتر که علاوه بر فشار محوری، فشار هیدرواستاتیک نیز به پودر وارد میشود. این تکنیک، تخلخل را به حداقل رسانده و قطعاتی با استحکام و خواص مکانیکی بسیار بالاتر به ارمغان میآورد.
- تف جوشی الکتریکی (EB): در این روش، انرژی حرارتی یک پرتو الکترونی متمرکز، پودر سیلیکون کارباید را ذوب میکند تا به شکل مطلوب درآید. این روش امکان ساخت قطعات پیچیده با دقت هندسی بالا را فراهم میکند.
- رشد بخار شیمیایی (CVD): روشی خاص که طی آن، سیلیکون کارباید از طریق واکنش بخارهای پیشماده بر روی یک بستر مناسب رسوب داده میشود. این روش تولید لایههای نازک و قطعات با ساختارهای میکرومتری را امکانپذیر میکند.
انتخاب روش تولید مناسب، تابعی از عوامل متعددی نظیر شکل قطعه، خواص مورد نیاز، میزان تولید و هزینه نهایی است. مهندسان خبره، با درک عمیق از خواص مواد و قابلیتهای هر روش، بهترین مسیر را برای خلق قطعات سیلیکون کارباید برمیگزینند.
فراتر از تولید: کنترل کیفی و تضمین کیفیت
تولید قطعات سیلیکون کارباید تنها با انتخاب مسیر درست پایان نمییابد. کنترل کیفی دقیق و پیوسته در تمامی مراحل، از تأمین مواد اولیه تا محصول نهایی، امری حیاتی است. تستهای سایندگی، مقاومت حرارتی، خواص الکتریکی و بررسیهای ریزساختاری، از جمله معیارهای تأیید کیفیت این قطعات حساس هستند.
شرکتهای معتبر تولیدکنندهی قطعات سیلیکون کارباید، بر رعایت استانداردهای بینالمللی و الزامات کیفی سختگیرانه تأکید دارند. این رویکرد تضمین میکند که محصول نهایی، متناسب با نیازهای صنایع مختلف و شرایط عملیاتی چالشبرانگیز، عملکردی استوار و ایمن را ارائه نماید.
افقهای درخشان: کاربردهای نوین و آیندهی امیدبخش
قطعات سیلیکون کارباید، امروزه طیف گستردهای از صنایع را متحول ساختهاند. از صنایع هوافضا و نیروگاههای برق گرفته تا صنایع فولاد، پتروشیمی و نساجی، این قطعات نقشی بیبدیل در افزایش کارایی، کاهش هزینههای تعمیر و نگهداری و ارتقای ایمنی ایفا میکنند.
تحقیقات و توسعههای مستمر در حوزه مواد و تولید، نویدبخش آیندهای درخشان برای قطعات سیلیکون کارباید است. توسعهی مواد مقاومتر در دماهای بالاتر، پیشرفت در روشهای تولید سریعتر و مقرونبهصرفهتر، و گسترش دامنهی کاربردها تنها بخشی از دستاوردهای بالقوهی این عرصه به شمار میروند.
به این ترتیب، میتوان با اطمینان گفت که قطعات سیلیکون کارباید، تنها قطعات مهندسیشدهی بیجان نیستند، بلکه آفرینشهایی مبتنی
تولید کننده قطعات لاستیکی و سیلیکونی
شرکت [پارس بسکنت]، پیشرو در تولید قطعات لاستیکی و سیلیکونی با کیفیتی بی نظیر، مفتخر است به همکاری با صنایع مختلف در راستای تامین قطعاتی مقاوم، ایمن و دقیق. از واشرهای ساده گرفته تا دیافراگمهای پیچیده، مجموعه گستردهای از محصولات ما پاسخگوی نیازهای طیف وسیعی از صنایع مانند:
- صنایع خودرو: قطعاتی همچون اورینگ، گسکت، بوش و ضربه گیر، با مقاومت سایشی و حرارتی بالا، عمر طولانی و عملکردی ایمن را در سیستمهای خودرو تضمین میکنند.
- صنایع نفت و گاز: قطعاتی با تحمل فشار و دماهای شدیدا حساس، از تجهیزات حیاتی صنعت محافظت میکنند و ریسک نشت مواد خطرناک را به حداقل میرسانند.
- ماشینسازی و تجهیزات صنعتی: از کوپلینگهای ارتعاشگیر تا روکشهای غلتک و نوار نقاله، قطعات لاستیکی و سیلیکونی، صلابیت و طول عمر تجهیزات صنعتی را افزایش میدهند.
- صنایع پزشکی و دارویی: قطعاتی با درجهبندیهای بهداشتی خاص، با سطوح استریل و تحمل مواد شیمیایی، نیازمندیهای حساس صنایع مرتبط با سلامت را برآورده میسازند.
- لوازم خانگی و آشپزخانه: از واشرهای درب تا درزگیرهای اجاق گاز، قطعات ما با خواص عایقبندی، تحمل حرارت و سادگی شستشو، آسایش و کارایی لوازم خانگی را تضمین میکنند.
تخصصص و نوآوری: رمز برتری ما
ما اعتقاد داریم کیفیت، تنها با تکیه بر دانش تخصصی و بهکارگیری فناوریهای نوین حاصل میشود. به همین دلیل، از تیمی باتجربه از مهندسین پلیمر و طراحان قالب بهره میبریم که همواره در راستای توسعه ترکیبات لاستیکی و سیلیکونی بهینه و طراحی قالبهای دقیق، تلاش میکنند. این رویکرد تضمینکنندهی:
- کیفیت و دوام بینظیر: ترکیبات لاستیکی و سیلیکونی با فرمولاسیونهای اختصاصی، بالاترین استانداردهای کیفیتی را برآورده میکنند و طول عمر قطعات را افزایش میدهند.
- دقت ابعادی بالا: طراحی و ساخت قالبهای پیشرفته، صحت ابعادی و عملکرد بینقص قطعات را تضمین مینمایند.
- پاسخگویی به نیازهای سفارشی: توانایی تولید قطعات سفارشی و مهندسیشده، متناسب با نیازهای خاص هر صنعت و پروژه را داریم.
- تحویل به موقع و کنترل دقیق کیفیت: سامانه مدیریت تولید کارآمد و نظارت سختگیرانه بر مراحل تولید، به ما امکان تحویل به موقع و کیفیت محصول در سطحی جهانی را میدهد.
همکاری با شما: سفری به سوی عملکرد بهینه
ما بر این باوریم که همکاری نزدیک با مشتریان، کلید دستیابی به بهترین نتایج است. از همین رو، کارشناسان متخصص ما همواره آمادهاند تا:
- با درک دقیق نیازهای شما، بهترین راهکارهای ترکیبات و طراحی قطعات را پیشنهاد دهند.
- نمونههای اولیه را مطابق با خواستههایتان تولید و عرضه نمایند.
- در مراحل نصب و نگهداری قطعات، پشتیبانی فنی دقیق ارائه دهند.
با انتخاب [پارس بسکت]، اطمینان حاصل کنید که قطعات لاستیکی و سیلیکونی با کیفیتی بیرقیب، عملکرد و طول عمر محصولات و تجهیزات شما را ارتقا دهند.
تماس با ما: اولین قدم به سوی بهبود
برای دریافت مشاوره رایگان و اطلاع از جزئیات محصولات و خدمات، همین امروز با ما تماس بگیرید. با افتخار در مسیر موفقیت در کنار شما خواهیم بود.
سفارش قطعات سیلیکونی
سیلیکون، متریالی شگفتانگیز با خواصی منحصربهفرد، امروزه در طیف گستردهای از صنایع، نقشآفرینی میکند. از صنایع پزشکی و غذایی گرفته تا هوافضا و خودروسازی، قطعات سیلیکونی با انعطاف، مقاومت و تحمل دمایی بالا، به قطعاتی کلیدی بدل شدهاند. اما سفارش این قطعات ظریف و خاص، دقت و دانش ویژهای میطلبد. در این راهنما، با اصول سفارش قطعات سیلیکونی آشنا شده و سفارشی مطمئن و کارآمد را تجربه خواهید کرد.
۱. نیاز خود را به درستی تعریف کنید:
- کاربری قطعه: برای چه مصرفی و در چه صنعتی به قطعه سیلیکونی نیاز دارید؟ مشخصات فنی و استانداردهای مورد نیاز را تعیین کنید.
- ابعاد و طراحی: شکل، اندازه، ضخامت و نوع اتصال قطعه را با دقت بیان کنید. نمونه یا نقشه فنی دقیق ارائه دهید.
- خواص فیزیکی و شیمیایی: سختی، مقاومت حرارتی، انعطافپذیری، تحمل مواد شیمیایی و رنگ مورد نظر را مشخص کنید.
۲. انتخاب تأمینکننده مناسب:
- تجربه و تخصص: از سابقه و تخصص تولیدکننده در ساخت قطعات سیلیکونی مشابه محصول مورد نظر خود اطمینان حاصل کنید.
- استانداردهای کیفی: تأمینکنندهای را انتخاب کنید که دارای گواهینامههای کیفی معتبر، مطابق با استانداردهای مورد نیاز شما باشد.
- ظرفیت تولیدی و زمان تحویل: توانایی تأمینکننده در تولید قطعات با تعداد، کیفیت و زمان تحویل درخواستی را بررسی کنید.
۳. مشخصات فنی قرارداد:
- مواد اولیه: نوع سیلیکون مصرفی، مانند سیلیکون خوراکی، پزشکی یا نسوز را در قرارداد ذکر کنید.
- تکنیک تولید: مشخص کنید که قطعه با قالبگیری فشاری، تزریقی، ریفلو یا تکنیک دیگری تولید میشود.
- کنترل کیفیت: مراحل کنترل کیفیت و تستهای مورد نظر را قبل از تحویل نهایی تعیین کنید.
- شرایط پرداخت و گارانتی: نحوه پرداخت، ضمانتنامه کیفیت و شرایط عودت کالا را بهصورت شفاف در قرارداد درج نمایید.
۴. نکات تکمیلی:
- حداقل سفارش: بسیاری از تولیدکنندگان، حداقل تعداد سفارش را برای پذیرش آن تعیین میکنند. از میزان حداقل سفارش مطلع شوید.
- نمونه اولیه: قبل از تولید انبوه، ساخت نمونه اولیه برای تست و تأیید نهایی توصیه میشود.
- خدمات پس از فروش: از خدمات پس از فروش و پشتیبانی فنی تأمینکننده اطمینان حاصل کنید.
با رعایت این اصول و توجه به جزئیات، میتوانید سفارشی مطمئن و مطابق با نیاز خود برای قطعات سیلیکونی انجام دهید. فراموش نکنید که تحقیق دقیق، انتخاب تأمینکننده مناسب و انعقاد قراردادی شفاف، کلید موفقیت در این مسیر است.
تولید محصولات سیلیکونی
سیلیکون، عنصر شگفت انگیزی در جدول تناوبی، نه تنها پایه و اساس ریزتراشه های پیشرفته است، بلکه دنیایی پویا از محصولات بی نظیر را نیز به وجود آورده است. محصولات سیلیکونی، با خواص منحصربهفرد خود، در صنایع مختلف نفوذ کردهاند و طیف وسیعی از کاربردها را به خود اختصاص دادهاند.
ویژگیهای متمایز محصولات سیلیکونی:
- مقاومت در برابر دما: محصولات سیلیکونی، چه در سرماهای شدید قطبی و چه در گرمای سوزان کورههای صنعتی، با ثبات و انعطافپذیری بینظیری عمل میکنند. این ویژگی، آنها را برای استفاده در محیطهای با شرایط دمایی خاص ایدهآل ساخته است.
- دوام و پایداری: محصولات سیلیکونی، نسبت به خوردگی، سایش و پارگی مقاوم بوده و عمر طولانی دارند. این ویژگی باعث کاهش هزینههای تعویض و نگهداری آنها میشود.
- ایمنی و سازگاری زیستی: سیلیکون، مادهای غیرسمی و زیستسازگار است و به ندرت باعث واکنشهای آلرژیک میشود. این ویژگی، استفاده از محصولات سیلیکونی را در صنایع مربوط به سلامت و بهداشت، ایمن و مطمئن کرده است.
- عایق الکتریکی عالی: خواص عایق الکتریکی و حرارتی بینظیر سیلیکون، آن را در صنعت برق و الکترونیک به گزینهای پیشرو تبدیل کرده است. از محصولات سیلیکونی در انواع سیمها، کابلها، واشرها و عایقهای حرارتی بهره گرفته میشود.
- انعطافپذیری و شکلپذیری: علاوه بر استحکام بالا، محصولات سیلیکونی از انعطافپذیری بالایی برخوردار بوده و به راحتی فرم میگیرند. این ویژگی، امکان تولید طیف وسیعی از محصولات با اشکال و اندازههای متنوع را فراهم میکند.
تنوع کاربردی محصولات سیلیکونی:
- صنایع پزشکی: لولههای تنفسی، ایمپلنتهای سیلیکونی، پستانک و سرنگ، تنها برخی از محصولات سیلیکونی پرکاربرد در بخش پزشکی هستند.
- صنایع غذایی: ظروف پخت و پز سیلیکونی، واشرهای آببندی و لولههای انتقال مواد، با حفظ سلامت و بهداشت، نقش مهمی در این صنعت ایفا میکنند.
- صنایع خودروسازی: واشرهای درب و پنجره، شیلنگهای رادیاتور و قطعات موتور، از جمله کاربردهای پرشمار محصولات سیلیکونی در صنعت خودرو هستند.
- صنایع ساختمانی: عایقهای درز و پنجره، درزگیرهای سیلیکونی و واشرهای ضدآب، به افزایش بهرهوری انرژی و کاهش اتلاف گرما در ساختمانها کمک میکنند.
- لوازم خانگی: ظروف پخت و پز سیلیکونی، ظروف کودک، لوازم آشپزخانه و ورزشی، تنها بخشی از کاربردهای گسترده محصولات سیلیکونی در زندگی روزمره هستند.
با توجه به خواص منحصربهفرد و کاربردهای متنوع، محصولات سیلیکونی جایگاه ویژهای در دنیای مدرن پیدا کردهاند. آنها به ارتقای کیفیت زندگی، بهبود کارایی در صنایع مختلف و حفظ سلامت محیط زیست کمک میکنند.
لازم به ذکر است که این متن صرفاً مقدمهای بر دنیای گسترده محصولات سیلیکونی است. برای هر یک از کاربردهای ذکر شده، طیف وسیعی از محصولات با ویژگیهای خاص وجود دارد. امید است این متن، نگاهی کوتاه و جامع به این محصولات شگفتانگیز ارائه کرده باشد.
تولید سیلیکون رابر
سیلیکون رابر، مادهای پلیمری با خواص منحصر به فرد، نقش به سزایی در صنایع مختلف ایفا میکند. از مقاومت حرارتی بالا و انعطافپذیری فوقالعاده گرفته تا پایداری شیمیایی و خواص عایقبندی عالی، این ماده کاربردهای متنوعی پیدا کرده است. در این نوشتار، نگاهی عمیق به فرآیند تولید سیلیکون رابر انداخته و با انواع روشهای ساخت و حوزههای مصرفی آن آشنا میشویم.
روشهای تولید سیلیکون رابر
به طور کلی، دو روش اصلی برای تولید سیلیکون رابر وجود دارد:
1. فرآیند پخت با پلاتین (Platinum Curing): در این روش، پلیسیلوکسانهای خطی (Si-O-Si) با سیلانهای دارای گروههای پلاتین واکنش داده و اتصال عرضی (Cross-Linking) بین زنجیرههای پلیمری صورت میگیرد. این فرآیند در دمای اتاق انجام شده و منجر به تولید سیلیکون رابرهای HTV (Vulcanizing at Room Temperature) با خواصی همچون شفافیت، انعطافپذیری بالا و دقت ابعادی میشود.
2. فرآیند پخت با پراکسید (Peroxide Curing): در این روش، از پراکسیدهای آلی به عنوان عامل پخت استفاده میشود. واکنش پخت معمولاً تحت حرارت صورت گرفته و منجر به تولید سیلیکون رابرهای LSR (Liquid Silicone Rubber) با ویژگیهای مقاومت حرارتی و شیمیایی فوقالعاده میگردد.
علاوه بر این دو روش اصلی، فرآیندهای دیگری نیز برای تولید سیلیکون رابرهای با خواص خاص و مصارف صنعتی ویژه توسعه یافتهاند که شرحشان در این مقال کوتاه نمیگنجد.
انواع سیلیکون رابر
بسته به نوع سیلانهای اولیه و افزودنیهای مورد استفاده، سیلیکون رابرهای مختلفی با خواص و ویژگیهای متمایز تولید میشوند.
- HTV سیلیکون رابر: این نوع سیلیکون رابر در دمای اتاق پخت شده و در تولید اجزای ظریف، قطعات عایقبندی، لوازم بهداشتی و پزشکی کاربرد دارد.
- LSR سیلیکون رابر: این نوع با مقاومت حرارتی بالا و استحکام کششی عالی، جهت ساخت قطعات خودرو، لوازم پختوپز و تجهیزات الکترونیکی مورد استفاده قرار میگیرد.
- RTV سیلیکون رابر: این نوع خاصیت چسبندگی بالایی داشته و در درزگیری، قالبگیری و ساخت واشرهای سیلیکونی به کار میرود.
کاربردهای متنوع سیلیکون رابر
سیلیکون رابر به دلیل انعطافپذیری، پایداری حرارتی و شیمیایی، زیستسازگاری و خواص عایقبندی بینظیر، در طیف وسیعی از صنایع کاربرد دارد:
- صنعت پزشکی: پروتزهای سیلیکونی، کاتتر، لولههای تنفسی، لنزهای تماسی
- صنعت خودروسازی: قطعات عایقبندی موتور، واشر، شیلنگ، تایر
- صنعت هوافضا: واشرهای مقاوم به دما، پوششهای محافظ حرارتی
- صنعت الکترونیک: کیپدهای صفحه کلید، عایقهای مدار چاپی، سیلانتهای ضد رطوبت
- صنایع غذایی: ظروف پختوپز، واشرهای درب قوطی، شیلنگهای انتقال مواد غذایی
- لوازم خانگی: دستگیرههای عایق، واشرهای در و پنجره، قالبهای یخ
همانطور که مشاهده شد، تولید سیلیکون رابر فرآیندی با اهمیت بالا و محصولات نهایی آن نقش کلیدی در صنایع مختلف ایفا میکنند. درک عمیق از مراحل تولید، انواع و کاربردهای سیلیکون رابر به مهندسان، متخصصان و فعالان صنعتی این امکان را میدهد تا انتخابی آگاهانه در بهرهگیری از این ماده شگفتانگیز داشته باشند.
خدمات تزریق سیلیکون
تزریق سیلیکون، فرآیندی پیشرفته و کارآمد برای تولید قطعات با دقت بالا و خواص منحصر به فرد است. این تکنولوژی، سیلیکون مایع را تحت فشار کنترل شده به درون قالبهای مخصوص تزریق میکند و طیف وسیعی از قطعات صنعتی، پزشکی، خودروسازی و غیره را ایجاد میکند.
مزایای برجسته تزریق سیلیکون:
- دقت و کیفیت بالا: تزریق سیلیکون با کنترل دقیق دما، فشار و زمان، قطعاتی با ابعاد و کیفیت سطح بسیار بالا تولید میکند.
- انعطافپذیری و مقاومت: سیلیکون، مادهای انعطافپذیر و مقاوم در برابر حرارت، کشش، سایش و مواد شیمیایی است و برای محیطهای چالشبرانگیز مناسب است.
- تنوع گسترده کاربردها: از واشرهای کوچک تا پروتزهای پزشکی، طیف وسیعی از قطعات را میتوان با استفاده از تزریق سیلیکون تولید کرد.
- سرعت تولید بالا: فرآیند تزریق سیلیکون نسبت به برخی روشهای قالبگیری سنتی، سرعت تولید بیشتری را ارائه میدهد.
- ایمنی و biocompatibility: سیلیکونهای مورد استفاده در تزریق، اغلب زیست سازگار بوده و برای تماس با مواد غذایی و دارویی مناسب هستند.
کاربردهای متنوع خدمات تزریق سیلیکون:
- صنایع پزشکی: پروتزهای سیلیکونی، لولههای تنفسی، قطعات دستگاههای پزشکی، ایمپلنتهای قابل انعطاف، عاج مصنوعی و …
- صنایع خودروسازی: واشرها، درزگیرها، قطعات داخلی کابین، قطعات مقاوم به حرارت و فشار مانند رادیاتور و …
- صنایع لوازم خانگی: دستگیرههای ظروف آشپزخانه، واشرهای ماشین لباسشویی، عایقبندی حرارتی لوازم خانگی و …
- صنایع الکترونیک: کیپدهای کنترل، عایقهای حرارتی و حفاظتی، اتصالات سیلیکونی، قطعات ضد ضربه و …
- صنایع هوافضا: قطعات عایقبندی حرارتی، قطعات مقاوم در برابر شرایط محیطی خاص و …
- صنایع ساختمانی: عایقهای در و پنجره، واشرهای سیلیکونی، قطعات ضدآب و …
انتخاب متخصصیترین خدمات تزریق سیلیکون:
انتخاب یک شرکت معتبر و باتجربه در زمینه تزریق سیلیکون، امری ضروری است. عواملی همچون، استفاده از دستگاههای بهروز، کنترل دقیق فرآیند، استفاده از مواد اولیه مرغوب، دارا بودن تجربه در تولید قطعات مختلف و خدمات پس از فروش مناسب، از معیارهای انتخاب یک شرکت مطمئن است.
نتیجهگیری:
خدمات تزریق سیلیکون، با ارائه ترکیبی ایده آل از دقت، سرعت، کیفیت و هزینه مقرونبهصرفه، گزینهای پیشرو برای تولید قطعات در صنایع مختلف محسوب میشود. با درک صحیح از مزایا و کاربردهای این تکنولوژی، انتخاب مناسب شرکت تأمینکننده خدمات و توجه به کیفیت مواد و فرآیند تولید، میتوان از پتانسیلهای شگفتانگیز این روش برای تولید قطعاتی دقیق، باکیفیت و انعطافپذیر بهرهمند شد.
تولید قطعات لاستیکی
تولید قطعات لاستیکی | لاستیک، متریالی شگفت انگیز با خواصی انعطاف پذیری، مقاومت سایشی، عایق بندی و ارتعاش گیری، نقش بسزایی در صنایع مختلف ایفا می کند. قطعات لاستیکی تولید شده، همچون رگ های حیاتی، در پیکره ماشین آلات و تجهیزات صنعتی جریان دارند و عملکرد صحیح آنها را تضمین می نمایند. از واشرهای ساده تا غلتک های غول آسا، تولید قطعات لاستیکی صنعتی یک فرآیند دقیق و تخصصی است که نیازمند دانش مهندسی و تکنولوژی پیشرفته می باشد.
مراحل اساسی تولید قطعات لاستیکی
تولید قطعات لاستیکی، سفری از مواد اولیه تا کالای نهایی را در بر می گیرد که متشکل از مراحل زیر است:
1. طراحی و مهندسی: این مرحله، سنگ بنای تولید است. مهندسین، با در نظر گرفتن کاربرد نهایی قطعه، نوع لاستیک، ابعاد و خواص فیزیکی و مکانیکی مورد نیاز، نقشه های فنی دقیق را تهیه می کنند.
2. فرمولاسیون و اختلاط: قلب تپنده قطعه، ترکیب لاستیکی بهینه است. مهندسین شیمی، با بهره گیری از دانش و تجربه خود، فرمولاسیون های اختصاصی با ترکیب مواد پایه لاستیکی، فیلرها، مواد تقویت کننده و افزودنی های ویژه را برای هر قطعه تهیه می نمایند. اختلاط دقیق این مواد، تحت حرارت و فشار کنترل شده، منجر به تولید خمیر لاستیکی یکدست و همگن می شود.
3. فرآیند شکل دهی: خمیر لاستیکی آماده، بسته به نوع قطعه مورد نظر، از طریق روش های مختلفی همچون:
- قالب گیری فشاری: برای تولید قطعات مسطح و ساده مانند واشرها و دیافراگم ها
- قالب گیری تزریقی: برای تولید قطعات با هندسه های پیچیده
- اکستروژن: برای تولید قطعات با مقاطع ثابت مانند تسمه ها و لوله ها
- قالب گیری انتقالی: برای تولید قطعات حجیم و توخالی با سطوح داخلی و خارجی صاف
به شکل نهایی خود در می آید.
4. پخت و ولکانیزاسیون: مرحله نهایی و حیاتی، پخت و ولکانیزاسیون است. در این مرحله، خمیر شکل دهی شده تحت شرایط حرارتی و فشار کنترل شده قرار می گیرد تا پیوندهای عرضی بین مولکول های لاستیک ایجاد شود. این فرآیند، خواص نهایی همچون استحکام، کشش و مقاومت حرارتی قطعه را تثبیت می نماید.
5. بازرسی و کنترل کیفیت: پس از پخت، قطعات تولیدی تحت بازرسی های دقیق فیزیکی و مکانیکی قرار می گیرند تا انطباق آنها با استانداردهای کیفی مطمئن گردد.
انواع لاستیک های مورد استفاده در قطعات صنعتی
طیف گسترده ای از لاستیک ها با خواص ویژه برای تولید قطعات صنعتی به کار می روند. برخی از رایج ترین انواع عبارتند از:
- لاستیک طبیعی: با انعطاف پذیری و مقاومت سایشی بالا، برای تولید انواع واشرها، یاتاقان ها و قطعات ارتعاش گیر مناسب است.
- لاستیک بوتادین استایرن (SBR): با ترکیبی از استحکام و قیمت مناسب، کاربرد گسترده ای در تولید تایر، تسمه و قطعات مقاوم به سایش دارد.
- لاستیک نیتریل (NBR): با مقاومت عالی در برابر روغن و سوخت، به انتخابی ایده آل برای واشرها و اورینگ های مورد استفاده در سیستم های هیدرولیک و پنوماتیک تبدیل شده است.
- لاستیک سیلیکون (Si): با تحمل دمای بالا و خواص عایق الکتریکی، برای تولید واشرها و درزگیرهای مورد استفاده در صنایع غذایی و پزشکی مناسب است.
نقش قطعات لاستیکی در صنایع مختلف
قطعات لاستیکی، به معنای واقعی کلمه، در هر صنعتی ردپایی دارند. از صنایع عظیم خودرو و هوافضا گرفته تا صنایع ظریف پزشکی و داروسازی، حضور این قطعات حیاتی است. برخی از کاربردهای کلیدی آنها عبارتند از:
- صنایع خودرو: تایرها، واشرها، یاتاقان ها، تسمه ها و قطعات ارتعاش گیر
- صنایع هوافضا: قطعات آب بند، شیلنگ ها و عایق های حرارتی
- صنایع نفت، گاز و پتروشیمی: واشرها
نحوه ساخت قطعات سیلیکونی
قطعات سیلیکونی به عنصری حیاتی در صنایع گستردهای مبدل شدهاند، از مراقبتهای بهداشتی و هوافضا تا خودروسازی و صنایع غذایی. ویژگیهای ذاتی سیلیکون، از جمله پایداری شیمیایی، مقاومت حرارتی، خواص ضدچسبندگی و انعطافپذیری، آن را برای طیف وسیعی از کاربردها ایدهآل میسازد.
در این مقاله، سفری عمیق را به دنیای تولید قطعات سیلیکونی آغاز میکنیم و فرآیندهای مختلف ساخت، مزایا و معایب هر روش و عوامل کلیدی موفقیت در تولید باکیفیت را بررسی میکنیم.
روشهای ساخت قطعات سیلیکونی:
- قالبگیری فشاری: روشی مقرونبهصرفه و مناسب برای تولید قطعات با هندسه ساده و تعداد بالا. سیلیکون با پیش کاتالیزور ترکیب شده و پس از افزودن رنگدانه در قالبهای تحت فشار شکل میگیرد.
- قالبگیری تزریقی: این روش برای ساخت قطعات پیچیدهتر و با نیاز به دقت ابعادی بالا مناسب است. سیلیکون مایع تحت فشار بالا به درون قالبهای گرم تزریق شده و شکل میگیرد.
- قالبگیری انتقال به رئومتر (RTM): برای قطعات تقویتشده با الیاف ایدهآل است. رزین سیلیکونی با فیبرهای بافتهشده توزیعشده در قالب، تحت فشار و حرارت قرار میگیرد تا شکل نهایی را به دست آورد.
- قالبگیری خلاء (VM): مناسب برای قطعات با دیوارههای نازک و سطوح ظریف است. خلاء هوا از حباب و نقص در قطعه نهایی جلوگیری میکند.
مزایای قطعات سیلیکونی:
- خواص شیمیایی و حرارتی مطلوب: مقاومت در برابر طیف گستردهای از مواد شیمیایی و دماهای بالا و پایین.
- عایق الکتریکی عالی: مناسب برای کاربردهای الکتریکی و الکترونیکی.
- انعطافپذیری و مقاومت به پارگی: عملکرد بهینه در محیطهای با ارتعاشات و سایش.
- راحتی رنگپذیری و قابلیت ایجاد سطوح بافتدار: افزایش جذابیت ظاهری و عملکرد قطعه.
- سازگاری زیستی مطلوب: ایمن برای تماس با مواد غذایی و بدن انسان.
معایب قطعات سیلیکونی:
- محدودیت تحمل بارهای سنگین: برای استحکام بالا نیاز به تقویت با الیاف یا دیگر مواد است.
- حساسیت به برخی حلالها و مایعات خاص: انتخاب نوع سیلیکون با توجه به شرایط محیطی ضروری است.
- هزینه قالبسازی اولیه بالا: برای تولید انبوه مقرونبهصرفه است، اما تولید محدود هزینهبر خواهد بود.
عوامل کلیدی موفقیت در تولید قطعات سیلیکونی:
- طراحی دقیق قالب: نقش حیاتی در کیفیت و دقت ابعادی قطعه دارد.
- انتخاب صحیح نوع سیلیکون: متناسب با خواص فیزیکی و شیمیایی مورد نیاز.
- کنترل دقیق فرآیند تولید: رعایت پارامترهای دما، فشار و زمان.
- بازرسی و تست نهایی: اطمینان از کیفیت و انطباق با استانداردهای لازم.
نتیجهگیری:
با انتخاب فرآیند تولید مناسب، مواد اولیه باکیفیت و رعایت اصول صحیح، ساخت قطعات سیلیکونی با عملکرد و دوام عالی امکانپذیر است. انعطافپذیری و ویژگیهای بینظیر سیلیکون، آیندهای درخشان را برای کاربردهای آن در صنایع مختلف ترسیم میکند.
امیدواریم این مقاله، دیدگاهی جامع نسبت به دنیای شگفتانگیز قطعات سیلیکونی در اختیار شما قرار داده باشد.
تولید کننده قطعات لاستیکی و سیلیکونی
شرکت پارس بسکت پیشرو در عرصه طراحی و تولید انواع قطعات لاستیکی و سیلیکونی با کیفیتی بی نظیر و برآورده سازی دقیق نیازهای صنایع گوناگون است. ما با تکیه بر دانش و تجربه متخصصان مجرب و بهره مندی از تکنولوژی های پیشرفته، طیف وسیعی از محصولات را مطابق با بالاترین استانداردهای بین المللی و نیازهای سفارشی مشتریان ارائه می دهیم.
پیشتازان نوآوری و کیفیت در دنیای پلیمرها
✔ طیف گسترده ای از محصولات: واشر، اورینگ، گسکت، دیافراگم، ضربه گیر، کوپلینگ، تسمه نقاله، قطعات صنعتی و بهداشتی و … تنها بخشی از محصولات متنوع ما هستند.
✔ انعطاف پذیری در تولید: قابلیت تولید قطعات با اشکال ساده و پیچیده، ابعاد و ضخامت های مختلف و با متریال متنوع لاستیکی و سیلیکونی
✔ کیفیت و دوام بی همتا: استفاده از مواد اولیه مرغوب و رعایت دقیق فرآیندهای تولید، عمر طولانی و عملکرد بهینه قطعات را تضمین می کند.
✔ کنترل کیفی دقیق: آزمایشات و بازرسی های مستمر در تمامی مراحل تولید، اطمینان از انطباق کامل محصولات با استانداردهای کیفی را به اثبات می رساند.
✔ مشاوره تخصصی: کارشناسان ما با اشراف کامل بر خواص مکانیکی و شیمیایی انواع لاستیک و سیلیکون، مشاوره دقیق و انتخاب مواد متناسب با هر کاربرد را در اختیار شما قرار می دهند.
✔ سرعت و دقت در تحویل: ما متعهد به رعایت دقیق زمانبندی های تحویل و ارسال محصولات با بسته بندی ایمن و مطمئن هستیم.
کاربرد محصولات ما در صنایع مختلف:
- صنایع خودروسازی: قطعات موتور، درب ها و پنجره ها، سیستم های تعلیق
- صنایع نفت و گاز: تجهیزات حفاری، قطعات آب بندی، واشرهای مقاوم به فشار و دما
- صنایع پزشکی و دارویی: قطعات سیلیکونی برای تجهیزات و ابزارهای پزشکی
- صنایع غذایی و آشامیدنی: واشرها و درزگیرهای بهداشتی، لوله های انتقال مواد
- صنایع ساختمان و عمران: عایق های رطوبتی، درزگیرهای درب و پنجره، قطعات ارتعاش گیر
- دیگر صنایع: لوازم خانگی، صنایع برق و الکترونیک، صنایع نظامی و هوافضا
برتری انتخاب یک تامین کننده معتبر قطعات لاستیکی و سیلیکونی
انتخاب یک تامین کننده معتبر و باتجربه در این حوزه نه تنها بر کیفیت و عملکرد قطعات مورد استفاده، بلکه بر بهینه سازی هزینه ها و پیشبرد روان پروژه های شما تاثیر بسزایی دارد.
ما در [ شرکت پارس بسکت] با درک این اهمیت، همواره بر ارائه خدماتی فراتر از تامین قطعات تمرکز داریم. مشاوره تخصصی، انتخاب مواد و طراحی دقیق، کنترل کیفی سختگیرانه و پشتیبانی فنی مستمر، تنها بخشی از تعهدات ما در قبال مشتریان ارزشمندمان است با [پارس بسکت ]، کیفیت، انعطاف و دوام را به پروژه های خود هدیه دهید.
منتظر تماس شما برای همکاری های موفق و سازنده هستیم.